In modern electronics manufacturing, soldering is a critical step in connecting components to the PCB.However, many engineers tend to focus only on the quality of the soldering itself, but ignore the long-term risks that flux residue after soldering can bring.This article reveals how flux residues can quietly affect the performance and reliability of electronic devices.
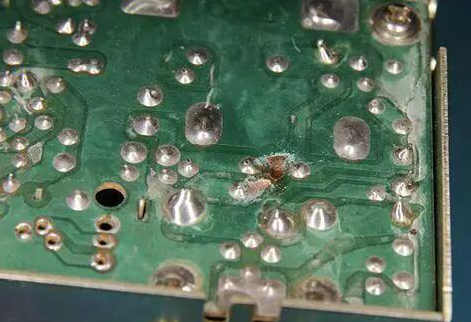
I. Double-sidedness of flux
Fluxes play an irreplaceable role in the soldering process:
- Removing metal surface oxides
- Reduce solder surface tension
- Prevent metal oxidation during soldering
However, once left behind, these “heroes” can be transformed into “invisible killers”.After the completion of the soldering, about 5-15% of the flux will be left on the circuit board, these residues seem harmless, but the hidden crisis.
II. The three major hazards of flux residue
1. Risk of electrochemical migration
Residual ionic substances (e.g. halogens, organic acids) can form conductive pathways in humid environments, resulting in:
- Leakage currents between neighbouring conductors
- Increased risk of short circuit
- Signal integrity degradation
2. Corrosion effects
Certain active ingredients continue to react with metal surfaces:
- Gradual corrosion of copper alignments
- Solder joint strength decreases over time
- Contact resistance increases
3. Degradation of insulation properties
Resin-based residues will:
- Reduce surface insulation resistance
- Affects high frequency signal transmission
- Causes signal crosstalk
III. How to deal with the threat of flux
1. Process control
- Selection of low residue no-clean fluxes
- Optimise soldering temperature profile
- Ensure adequate hot air levelling
2. Cleaning treatment
- Cleaning within 24 hours after welding
- Use a suitable cleaning agent (water-based or solvent-based)
- Pay attention to cleaning dead spots (e.g. bottom of QFN)
3. Testing and verification
- Ion contamination test
- Surface insulation resistance measurement
- Visual inspection with magnifying glass
IV. Conclusion
Flux residue is like a “chronic disease” in electronic products, which may not have obvious symptoms in the short term, but can lead to performance degradation and early failure in the long term.Through scientific process control and post-processing, we can minimise this hidden threat and ensure the long-term reliability of electronic products.While pursuing soldering efficiency, do not ignore these unseen risks, as the details often determine the final quality of the product.