With the development of the PCB industry, the impedance requirements of various conductors are becoming higher and higher, which inevitably requires stricter control of the width of the conductors. Widely used in life, the quality of PCB is getting better and more reliable, and its design process is becoming more and more diverse and perfect. Etching technology is also becoming more and more widely used in PCB design. Etching technology uses the photosensitive properties of chemical photosensitive materials to evenly apply photosensitive materials on both sides of the base metal substrate. Using the photolithography method, the shape of the grid on the film plate is accurately copied to the photosensitive layer mask on both sides of the metal substrate. The mask is developed to remove the non-photosensitive parts, and the exposed metal parts are etched away by direct pressure contact with the corrosive liquid during subsequent processing, and finally the required geometric shape and high-precision size of the product are obtained.
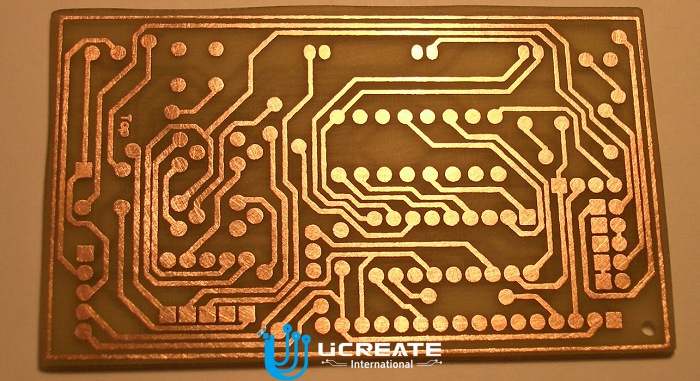
Introduction to PCB etching process
1. PCB etching process principle
Etching is to spray the etching liquid evenly onto the surface of the copper foil through a nozzle under certain temperature conditions (45+5), and undergo a redox reaction with the copper that is not protected by the etching resist, and the unnecessary copper reacts to expose the base. The material is then peeled off to form the circuit. The main ingredients of the etching solution: copper chloride, hydrogen peroxide, hydrochloric acid, soft water (there are strict requirements on solubility)
2. PCB etching process quality requirements and control points:
1)There should be no residual copper, especially double-sided panels.
2)There should be no residual glue, otherwise it will cause exposed copper or poor adhesion of the plating.
3) The etching speed should be appropriate, and thinning of the line caused by excessive etching is not allowed. The etching line width and total pitch should be the focus of the site’s management and control.
4) The dry film on the circuit solder joints must not be washed away, separated or broken.
5) The board after etching and peeling is not allowed to have oil stains, impurities, copper peeling and other bad qualities.
6)When placing the board, care should be taken to avoid jamming and oxidation.
7)The uniform distribution of the etching solution should be ensured to avoid uneven etching on the front and back sides or different parts of the same side.
3. PCB etching process control parameters
Etching solution temperature: 45+/-5℃, solubility of hydrogen peroxide 1.95~2.05mol/L
Stripping liquid temperature: 55+/-5°C. The safe operating temperature of the etching machine is ≤55°C.
Drying temperature: 75+/-5’℃ Spacing between front and rear plates: 5~10cm Specific gravity of copper chloride solution: 1.2~1.3q/cm3 Platen angle, guide plate, upper and lower nozzle switching status!
Hydrochloric acid solubility: 1.9~2.05mol/L
4. PCB etching process quality confirmation
Line width: Etching standard lines are .2mm & 0.25mm, which must be within +/-0.02mm after etching
Surface quality: No wrinkles, scratches, etc.
There should be no residual copper when inspected by light transmission.
Lines cannot be deformed
No oxidized water droplets
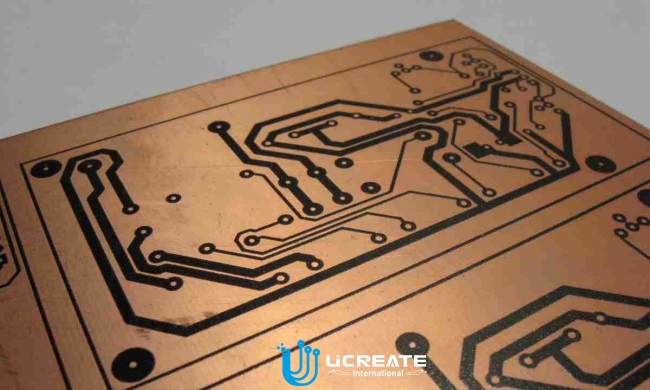
PCB etching process detailed explanation The etching process is: film stripping → circuit etching → tin and lead stripping

Peel off the film
Film stripping is used in two steps in the PCB process. One is D/F stripping after the inner layer circuit is etched, and the other is D/F stripping before the outer layer circuit is etched (if the outer layer is made as a negative film process) D The stripping of /F is a simple and simple process. Generally, horizontal equipment is used. The chemical liquid used is mostly NaOH or KOH with a concentration of 1~3% by weight. Things to note are as follows:
1) The hardened dry film is partially dissolved in this solution and partially peeled into flakes. In order to maintain the effect of the liquid medicine and ensure thorough washing, the efficiency of the filtration system is very important.
2) Some equipment is designed with light brushing or ultrasonic stirring to ensure the thoroughness of the film, especially when peeling off the film after the outer layer is etched. The dry film that is slightly stuck by the secondary copper on the line side must be completely peeled off to avoid affecting the line quality. . BCS is also added to the solution to help dissolve it, but it is against the environment and harmful to the human body.
3) Some literature states that K (potassium) will attack tin, [therefore the selection of stripping liquid before outer layer circuit etching must be carefully evaluated. The peeling liquid is alkaline, so it is very important to wash it thoroughly. After peeling off the inner layer, pickling is added to neutralize it, or the copper surface is oxidized to prevent oxidation.
Circuit etching
1. Mechanism that corrodes copper
(1) In an alkaline environmental solution, copper ions easily form the precipitation of copper hydroxide. It is necessary to add enough ammonia water to generate ammonia copper ion groups, which can inhibit the occurrence of precipitation and at the same time reduce the original amount of copper. And the copper that continues to dissolve forms very stable ammonia copper ions in the liquid. This divalent ammonia copper ion can also be used as an oxidant to oxidize and dissolve the zero-valent metallic copper. However, there will be a one-valent copper ion during the redox reaction. Cuprous ions) appear.
That is to say, the solubility of the intermediate cuprous ion in this reaction is very poor. It must be assisted by ammonia water, ammonia ions and a large amount of oxygen in the air to continue to oxidize it into soluble divalent copper ions, and then become an oxidant that corrodes copper, and the cycle starts again. Continue to etch copper until there is too much copper and it slows down. Therefore, in addition to removing the ammonia odor, the exhaust of the general etching machine can also provide fresh air to accelerate copper etching.
(2) In order to make the above-mentioned copper etching reaction proceed more quickly, add more additives to the etching solution, such as:
a. The accelerator Acceletator can promote the above-mentioned oxidation reaction more quickly and prevent the precipitation of cuprous ions.
b. Banking agent reduces side erosion.
c. Suppressor inhibits the scattering of ammonia at high temperatures, inhibits the precipitation of copper, and accelerates the oxidation reaction of copper corrosion.
2. Equipment
(1) In order to increase the corrosion rate, the temperature needs to be raised to above 48°C. Therefore, there will be a large amount of ammonia odor permeating the air and proper ventilation must be carried out. However, if the ventilation volume is too strong, a large amount of useful ammonia will be removed. It is very uneconomical. An appropriate throttle valve can be added to the exhaust pipe for control.
(2) The etching quality is often limited by the pool effect (pudding) (because the fresh chemical solution is blocked by the accumulated water and cannot effectively react with the copper surface, which is called the pool effect). This is why the front end of the board often has an over etch phenomenon. Therefore, there are following considerations in equipment design:
a. The thinner lines on the board face down, and the thicker lines face up. b. Adjust the upper and lower spray pressures of the nozzle to compensate, and adjust the difference according to the actual operating results.
c. The advanced etching machine can control how many seconds the first groups of nozzles will stop spraying when the board enters the etching section.
d. There are also vertical etching methods designed to solve the problem of unevenness on both sides, but it is rarely used in China. Currently, there is a self-made vertical etching machine produced by Kemao Company in use in China.
Send PCB Files to Sales@ucpcba.com, We Will Quote You Very Soon!
3. Add additional controls
Automatic replenishment: The replenishing liquid is ammonia, usually with an extremely sensitive hydrometer, which senses the current temperature (due to differences in specific gravity at different temperatures), sets upper and lower limits, and starts adding ammonia when it is higher than the upper limit, and does not stop until it is lower than the lower limit. At this time, the position of the detection point and the position of the nozzle for adding ammonia are very important to avoid wasting costs by adding too much ammonia due to detection delay (because it will overflow)
4. Daily maintenance of equipment
(1) Prevent the etching solution from producing sludge (light blue monovalent copper sludge), so component control is very important – especially the PH, which may be caused by being too high or too low.
(2) Keep the nozzle from being clogged at all times. (The filtration system must be kept in good condition)
(3) The specific gravity induction adding system must be calibrated regularly.
Stripping tin (lead)
Regardless of the pure tin or the tin-lead layer with various composition ratios, the purpose of plating is only to resist etching. Therefore, it must be stripped after the etching is completed. Therefore, this tin (lead) stripping step is only processing and does not generate additional value. . However, special attention must be paid to the following points, otherwise the cost will increase secondly, and the outer circuit will be completed with great difficulty but cause defects here.
1. Generally, tin (lead) stripping liquid is supplied directly from the supplier. There are many formulas, including two-liquid type and single-liquid type. The stripping method includes semi-soluble type and fully soluble type. The composition of the solution is fluorine system/H202HNO3 /H202 and other formulas.
2. Regardless of the formula, there are the following potential problems in operation
a. Attack the copper surface.
b. The incomplete stripping affects the post-processing process.
c. Waste liquid treatment issues
Therefore, the tin (lead) stripping step must rely on good equipment design, control of the tin (lead) thickness in the previous process, and management of the efficacy of the liquid to achieve stable quality. After the outer circuit is produced, 100% inspection is performed.
Basis for judging the quality of etching conditions
1. Protruding edge
2. Side erosion
3. Etching coefficient factor
4. Over corrosion
5. Etching surface finish
6. Is the line spacing clear?
With the miniaturization of electronic products, the lines of circuit boards are moving toward thin lines, high density, and fine apertures, which puts higher requirements on the etching process.