Basic knowledge of copper-based PCB
2. Generally, there are immersed gold copper circuit board, silver-plated copper scircuit board, tin-sprayed copper board, anti-oxidation copper board etc. The circuit layer of the copper PCB is required to have a large current-carrying capacity, so thicker copper foil should be used, with a thickness of generally 35 μm to 280 μm; the thermal insulation layer is the core technology of the copper PCBs, and the core thermal conductive components are aluminum oxide and silicon powder. It is composed of polymers filled with epoxy resin, has small thermal resistance (0.15), excellent viscoelastic properties, has the ability to resist thermal aging, and can withstand mechanical and thermal stress. The metal base layer of the copper printed circuit board is the supporting component of the copper PCB and requires high thermal conductivity. It is usually a copper plate. Copper plates can also be used (copper plates can provide better thermal conductivity). They are suitable for conventional mechanical processing such as drilling, punching, and cutting. .
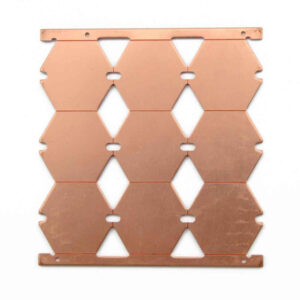
3.1 Base material
The base material of the copper PCB refers to the basic material that supports and fixes the copper foil. Common board include fiberglass cloth, ceramics, metal, etc. Glass fiber cloth substrate has good mechanical strength and heat resistance and is suitable for most electronic products. Ceramic substrates have excellent insulation properties and high-frequency characteristics and are often used in high-frequency circuits and microwave devices. Metal substrates have good thermal conductivity and mechanical strength and are suitable for power electronic devices and applications with high heat dissipation requirements.
3.2 Copper foil
Copper foil is an important part of copper PCB, and electrolytic copper foil is generally used. Electrolytic copper foil is prepared by electrolytic deposition and has good electrical conductivity and reliability. The thickness of copper foil is usually between 9um and 105um, and different application fields require different thicknesses of copper foil. Copper foil can provide a path for current transmission, and also plays a role in stabilizing and fixing the PCBs.
3.3 Protective layer
The protective layer of the copper PCB is a covering added to prevent oxidation, corrosion and mechanical damage to the copper foil. Common protective layers include organic coatings, inorganic coatings, solder plating coverage, etc. Organic coatings are usually coated with covering agents, which can provide certain insulation and anti-corrosion effects. Inorganic coatings generally use materials such as tin oxide and tin oxide plating, which have good electrical conductivity and high temperature resistance. Solder plating provides protection and soldering performance by covering a layer of tin-lead alloy.
3.4 Other components
In addition to the base material, copper foil and protective layer, the copper circuit board may also contain other components such as solder mask, printing layer, etc. The solder mask is a layer of covering added to avoid short circuits and protect circuits. Common materials include light-curing solder mask oil, heat-curing solder mask oil, etc. The printing layer is a coating added to facilitate the printing of circuit patterns. Common materials include carbon ink, silver paste, etc. The copper PCB structure includes base material, copper foil, protective layer and other elements. Different application fields and requirements will have different copper PCB structural designs to meet the needs of circuit transmission, insulation and protection. The rational design and preparation process of copper PCB structures have an important impact on the performance and reliability of electronic products. Therefore, attention should be paid to structural matching and optimization in the selection and application of copper-based boards. As an important basic material for electronic components, copper based printed boards will continue to play an important role in the electronic field.