Classification of medical PCB
With the continuous development of modern medical technology, more and more electronic devices are used in the medical field. Among them, PCB (printed circuit board), as basic parts in electronic equipment, are used more and more widely. Medical PCB boards are circuit boards used in the medical field. According to their properties and uses, medical printed circuit boards can be divided into the following categories:
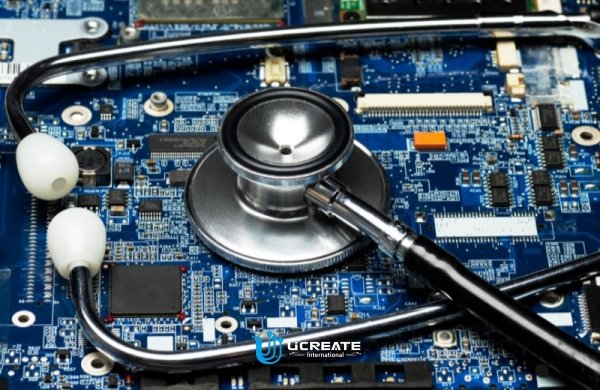
1. High frequency PCB
Medical equipment commonly used in the medical field, such as ultrasound, electrocardiograms, diagnostic instruments, etc., all require the use of high-frequency electronic circuits, and high-frequency circuits require the application of high-frequency PCB boards. Such as: low attenuation, low impedance, high reliability, etc. The requirements of high-frequency PCB boards manufacturing are very high, and professional technical support is required in terms of material selection, design specifications, and processing technology.
2.Amplifier PCB
Functional modules such as signal amplifiers and amplified sensors in medical equipment require the use of amplifier PCB boards. Compared with ordinary PCB boards, amplifier circuit boards need to have higher circuit accuracy and stability, and require special processing for signal isolation and anti-interference requirements. In practical applications, medical equipment needs to have high reliability and high precision, so the amplifier PCB board needs to be perfect in the PCB fabrication process.
3. EEG PCB
EEG is an important device for detecting brain electrical activity, and the EEG PCB board is an important part of the EEG device. EEG printed circuit boards need to have the characteristics of high stability and strict process control, patch electrical properties, high precision, low noise, and strong anti-interference. When manufacturing EEG PCBs, it is necessary to consider the design of the circuit layer and the selection of components such as capacitors.
4. Laser equipment PCB
Laser equipment is widely used in the medical field, such as laser therapeutic instruments, laser scalpels, laser detection instruments, etc. PCB boards related to laser equipment also need to have some special properties, such as high precision, high reliability, anti-interference, etc. When manufacturing and designing laser equipment PCB boards, special attention needs to be paid to the protection and assembly of optical components and the detection of laser radiation safety.
5. Other medical PCB
In addition to the above types of medical PCB boards, there are many other PCB board applications in medical equipment. For example, medical measurement equipment such as heart rate monitors, blood pressure monitors, and diabetes detectors all require the use of medical PCB boards. In addition, medical rigid boards,flex circuit board and rigid-flex boards are also used in medical imaging equipment, medical robots, medical surgical knives, etc. The PCB electronic boards required by these devices need to have different characteristics, so manufacturing medical PCB requires special design and manufacturing according to different needs.
In summary, medical PCB boards have special performance requirements. According to different uses and needs, special attention needs to be paid to their design, manufacturing, and testing. In view of the importance of medical PCB boards, companies that manufacture medical PCB boards also need to have professional of technical personnel and excellent production equipment to ensure the quality and safety of medical equipment.
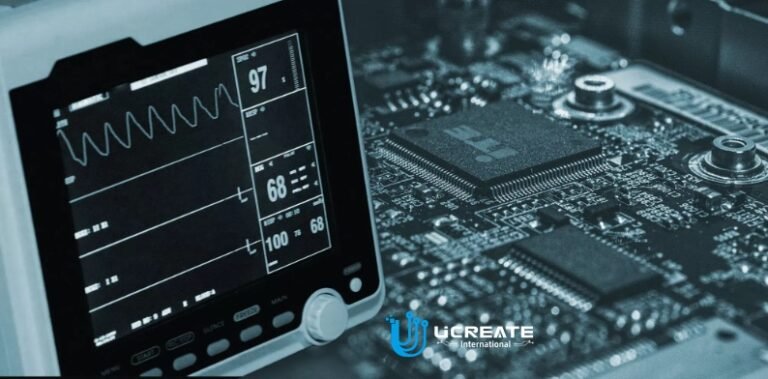
Before you prepare to produce medical PCBs, please take a look at the following points so that you can choose the best pcb manufacturer.
1.”Safety” and “reliability”: are the core issues of PCB boards in the medical industry. Life support products or high-end products refer to IPC-3 standards, and non-life support or mid- to low-end products refer to IPC-2. Large medical terminals have established their own independent and standardized corporate standards to strictly control product reliability. So this is very important.
2.Long service life: Generally, product warranty time is more than 5 years, and large medical equipment requires at least 10 years. At the same time, the product has a long service life. There are still differences between medical PCB and ordinary PCB.
3.Large span of levels: from consumer medical products that meet conventional requirements, to mid-to-high-end medical products that meet high reliability and stability requirements, to small portable products that meet high density and high integration, as well as smart Wearable medical products that are specialized and multi-functional.
4.Product conservatism: The application of new medical technologies and new products on the market is slow, and verification tests of new products are repeated, often requiring comprehensive evaluation.
5.Traceability: Products require strict process records and product traceability. Some large medical terminals require traceability of PCB processing records for 10 years.
6.The process processing and fire protection grade requirements of medical PCB boards are different. Ordinary PCB processes have different methods for spraying tin and cleaning the board. On the premise of taking technological measures and ensuring quality and safety, repair products can be used with caution as appropriate.
7.The demand for general medical PCBs is very small, but there are many process requirements, such as HDI, back drilling, multiple lamination, mixed pressure, high precision, special impedance, thick copper, thick gold, embedded copper blocks, etc. The price focus will be very low, which is also different from ordinary PCBs.
What should you pay attention to when wiring industrial medical double-sided PCB circuit boards?
1. Minimize the discontinuity of the industrial control medical double-sided PCB circuit board wires. For example, the wire width should not change suddenly, the corners of the wires should be greater than 90 degrees, and circular routing is prohibited.
2. Clock signal leads are most likely to cause electromagnetic radiation interference. Industrial control and medical double layer PCB circuit boards should be routed close to the ground loop, and the driver should be close to the connector.
3. The bus driver should be close to the bus it wants to drive. For those leads that exit the PCB, the driver should be located immediately next to the connector.
4.The wiring of the data bus of the industrial control medical 2 layer printed circuit board should sandwich a signal ground wire between every two signal wires. It is best to place the ground return immediately next to the least important address leads, which often carry high-frequency currents.
5.When arranging high-speed, medium-speed and low-speed logic circuits on printed boards, devices should be arranged.
Industrial control and medical double sided PCB boards suppress reflection interference. In order to suppress the reflected interference that appears at the terminals of printed lines, except for special needs, the length of printed lines should be shortened as much as possible and slow circuits should be used. If necessary, terminal matching can be added, that is, a matching resistor with the same resistance value can be added to the end of the transmission line to the ground and power supply ends. According to experience, for generally fast TTL circuits, terminal matching measures should be used when the industrial control medical double-sided PCB circuit board lines are longer than 10cm. The resistance of the matching resistor should be determined based on the maximum output drive current and absorption current of the integrated circuit.