During the SMT chip processing, static electricity mainly brings the following hazards:
- Component damage: Electrostatic discharge may cause sensitive electronic components such as integrated circuits, transistors and diodes to be electrically broken down or overloaded, resulting in loss of function. This damage may be sudden or may gradually appear in subsequent use, affecting the stability and life of the component.
- Equipment failure: Static electricity poses a threat to precision equipment and may cause electronic equipment on the production line to be paralyzed, affecting production efficiency. Electrostatic discharge can interfere with the normal operation of equipment and cause production interruptions.
- Production line stagnation: Static electricity problems can cause components on the production line to be damaged, affecting production progress. Component damage and equipment failure will cause the production line to stop production and replace parts, increasing costs and time.
- Component adsorption: Static electricity will adsorb electronic components, causing changes in the distance between components, affecting the positioning accuracy of SMT equipment, and thus affecting production quality.
- Product quality issues: Electrostatic discharge will leave hidden dangers inside the product, resulting in unstable product quality. Potential damage may cause frequent freezes, automatic shutdowns and other problems in subsequent use, affecting the reliability and service life of the product.
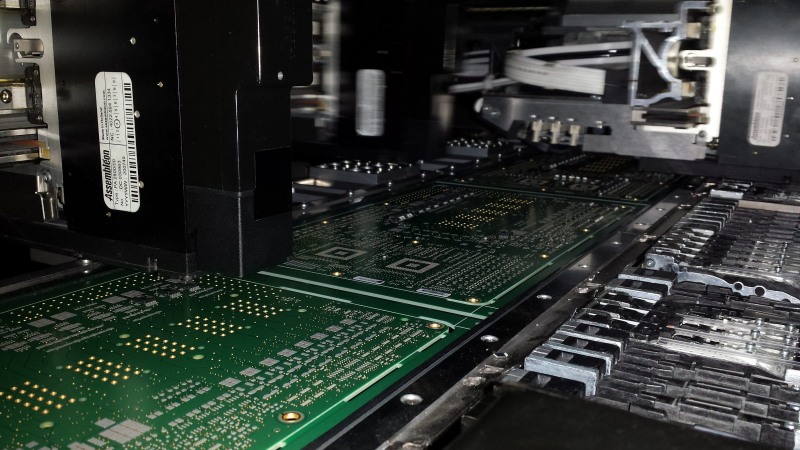
In order to reduce the impact of static electricity on SMT chip processing, the following measures can be taken:
- Use anti-static equipment and materials: Use anti-static workbenches, anti-static clothing and anti-static materials during SMT processing to reduce the generation and accumulation of static electricity.
- Grounding treatment: Ensure that equipment and personnel are grounded, reduce the accumulation and conduction of static electricity, and prevent static electricity from damaging equipment and components.
- Environmental control: Maintain the humidity and temperature of the processing environment to reduce the generation of static electricity. It is usually recommended to control the humidity of the workshop between 50% and 70% .
- Regular inspection and maintenance: Regularly check the effectiveness of anti-static equipment and materials to ensure their normal operation. At the same time, maintain the equipment to reduce static electricity problems caused by aging or damage of the equipment.
Through the above measures, the impact of static electricity on SMT chip processing can be effectively reduced, and production efficiency and product quality can be improved.